Environmental Impact
A common escalator that has a 7.5 horsepower motor,rising 15 feet above the ground,kept running 14 hours a day, six days a week will consume almost 7500 kilowatt hours (kWh) of electricity in a year. A larger escalator will consume almost 31000 kwH of electricity a year.
A continuously running escalator, such as those found in airports or subway stations are 35 feet high with a 40 horsepower motor. These escalators consume 60,000 kWh annually. (For a comparison, the average American home consumes 11,040 kWh in a year.)
KONE
The lifecycle assessments of KONE escalators show that the greatest environmental impact of an escalator stems from the electricity used in the operating the escalator.
Therefore, the key focus area for KONE is to systematically reduce the energy consumption of its escalator features with each new product release.
Escalators also consist mostly of metals and about 80% of this material can be recycled.

The energy-efficient NCE escalator from Otis offers customers substantial “green” benefits, including:
-
A ReGen™ drive that captures energy generated by the escalator on the way down and delivers it back to the building for use by other systems, reducing energy consumption by up to 45 percent compared to traditional escalators.
-
Power standby technology, which uses sensors that detect when passengers are not on the escalator, prompting the escalator to slow down and thereby use less energy.
-
LED lighting that uses 30 percent less energy than traditional lighting
-
High-efficiency lubrication that uses 98 percent less oil than a traditional lubrication system.
-
IntegraPower-E, created by Precision Labs, matches the appropriate power levels to the given load conditions. This electronic power optimization technique saves maximum energy in lightly loaded conditions without changing escalator operating speed. It enables the escalator to operate under a reduced voltage configuration. This reduces escalator energy consumption up to 50%

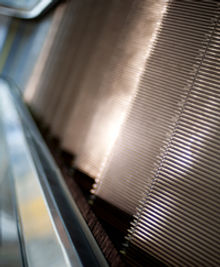

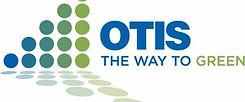

There are 4 ways that KONE has identified to make the escalator more eco-efficient
1) Having a lubrication-free step chain
The benefits of having this chain include an average oil savings of 1-2 liters a month for commercial escalators, and 5 litres for infrastructure escalators.
2) Having a regenerative solution
A regeneration of power, such as from the downward running of the passenger loaded escalator. These functions are available where an inverter is installed. From this, there will be energy savings of 7100kWh/year.
3) Having an eco-efficient operation
Functions include a Stop & Go operation, where the escalator stops running when not in use with almost no power consumption when escalator is stopped. There will be energy savings of almost 2760 kWh/year.
4) Having LED lighting
Having such lighting will result in energy savings of 1960 kWh/year compared to conventional lights





High-efficiency motors and drives
-
Schindler escalators come with high-efficiency motors and variable frequency drives, and also have the option of being installed with energy regenerative drives.
ECO energy-saving package option
-
Schindler’s 9300® Advanced Edition escalator features the ECO energy-saving packages, which may generate energy savings of up to 20 percent by providing soft start/stop functionality and reduction in peak current.
Eco-friendly details
-
The escalator packaging is recyclable and low-mercury high-efficiency compact fluorescent lighting is used. Water-based paints and powder coating are used to limit the emission of volatile organics into the environment.
Below are some examples of Environmentally Friendly Technology from the escalator companies
Schindler Escalator Technology

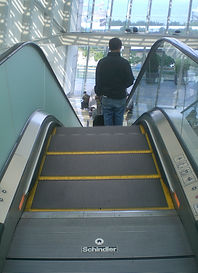